
University of Manchester - Manchester Engineering Campus Development (MECD)

About University of Manchester & the Manchester Engineering Campus Development (MECD)
The University of Manchester is on a mission to ‘advance education, knowledge and wisdom for the good of society’ by focusing on a collaborative culture, world-class research facilities and innovative teaching and learning spaces. To get closer to this goal, the University decided to bring all their academic activity together onto a single site; The Manchester Engineering Campus Development (MECD).
The Manchester Engineering Campus Development is the University of Manchester’s flagship project which aims to provide an environment that creates a sense of pride in the heritage and achievements of the University, while inspiring future generations of engineers to innovate and discover. The University’s vision for MECD is to provide a legacy that staff, students and alumni are proud of now and in the future, which would help improve the student experience, the running of the estate, and reduce the University’s carbon footprint.
It is one of the largest, single construction projects ever undertaken by a higher education institution in the UK, winning awards for the best use of IT in a Construction project and will transform the way the University educates engineers in response to the needs of the fast-changing global economy.
The Requirements
The university had a vision of implementing Building Information Modelling (BIM) and collating asset data during the design and build process. They recognised the benefits of digitising construction and putting digital workflows in place and were keen to take control of the models after the project is finished. They also wanted an accurate clash resolved model to help maintain the facilities going forward, storing all the data within their own CDE system.
They also needed to achieve this through their Better Buildings Initiative (BBI) which incorporates elements of the RIBA 2013 Plan of Works, the Soft Landings Framework, and the NEC contract philosophy into the design and contractor team duties. This would help deliver a building that will exceed the University’s estates, facilities and occupant expectations for sustainability, energy efficiency, manageability, maintainability and overall performance.
As the above requirements stipulated a BIM Level 2 approach, the key solution had to be a data rich model, with outputs in the correct formats to suit their data requirements. They also needed to take on a standard-setting and policing role for project.
The Solution
The University of Manchester appointed the role of “BIM and Information Manager” to Symetri in 2011 before PAS 1192 was introduced, to help create, manage and police a set of Employers Information Requirements (EIR’s) and Asset Information Requirements (AIR’s). This was to be used as a deliverable specification, checking and validation standard, and as a route to the receptors of the data in their space management and asset management tools.
Having worked closely with the team on the Graphene Institute to generate a schedule of required information, Symetri then produced a standardised EIR with the intention that it can be used as a default starting place for all works across the scheme.
“It's a highly complex building because it includes numerous laboratories and lecture spaces which makes the building services side of the project quite difficult.” explains Steve Rudge, Symetri BIM Manager on the MECD project.
The project was awarded to Balfour Beatty in 2017 who worked together with Symetri on the digital approach of the scheme from the initial clash detection process to design, technical design, through to field management. Together they performed an audit on each room of the building. This enabled all involved to see where the 3D model had been verified against the as-built state of the building.
“Identifying clashes was a task in itself. The fact that the main parties involved started discussions about the project early prevented information loss and ensured that this flowed seamlessly between the design and construction teams.” Steve added.
At the heart of the delivery was Autodesk’s BIM 360 which empowered the digital construction approach by digitally capturing quality, safety and commissioning checklists, work permits and routing inspections such as the site hording board inspection where progress and issues could be tracked and closed out.
NG Bailey was then appointed by Balfour Beatty, on behalf of the University of Manchester, to provide Mechanical Engineering & Plumbing (MEP) services across the MECD project.
Martin Hardman, Divisional Digital Engineering Manager at NG Bailey, explains the company's approach:
"Considering the size of the project, we wanted to create a BIM approach that allowed for the optimal levels of collaboration. Therefore, we decided to take a cloud-based approach using Autodesk’s BIM 360 for our BIM models, which meant that all relevant parties could work together seamlessly to bring the project to life."
Due to this approach, there was no need to redesign things which meant that NG Bailey could bring their services into modular construction. “This gave us confidence that all the services in the building will actually fit in.” explains Steve.
Balfour Beatty also appended a barcode to each piece of plant as soon as they arrived, associated it with a check sheet on the field, created a list of generic plan references on the equipment and listed them under the different types. As soon as the next piece came in, the person that was signing that piece of plant in would complete the check points. The check sheet, 360° photographs of the piece of plant, the serial number and then the daily checks against it would all be recorded. As the operator hands the check sheets back to the site manager, they will take a copy of that check sheet for that day.
“We were then able to link all of that fantastic data, photographs, anything we could append to those check sheets and trace back to establish whether there were ever any issues with any of those concrete items” concluded Balfour Beatty’s BIM Coordinator on the MECD project.
The Result
This collaborative workflow resulted in significant time savings:
- 15 hours saved a month – Model Federation
- 4 hours saved a month – Federating Comments
- 4 hours saved a month – Clash Reporting
Total: 276 Hours a year = around 36 days saved.
The MECD base build project has now been completed and the information has been handed back to the University of Manchester, delivered and migrated into their space and asset management systems.
The University have a set of requirements and processes in place that can be used to specify measure and operate the information management across all projects in this ambitious scheme. Symetri remain committed to building on this strong foundation and assisting the University to achieve its goals until scheme completion in 2022.
“The MECD project has proven that digital construction is the way forward” said Steve Rudge. “Working with all the parties involved, implementing a system that will benefit everyone is the formula for success. You should start putting processes in place only after engaging with the subcontractors and the supply chain partners and incorporating their feedback. Once this is done, you’ll be able to see the benefits of collaborative working and of the workflows implemented.”
Take the virtual tour of the finished project with some of the Balfour Beatty team in this video https://www.youtube.com/watch?v=mz6PYPqN-Ec.
Related Cases

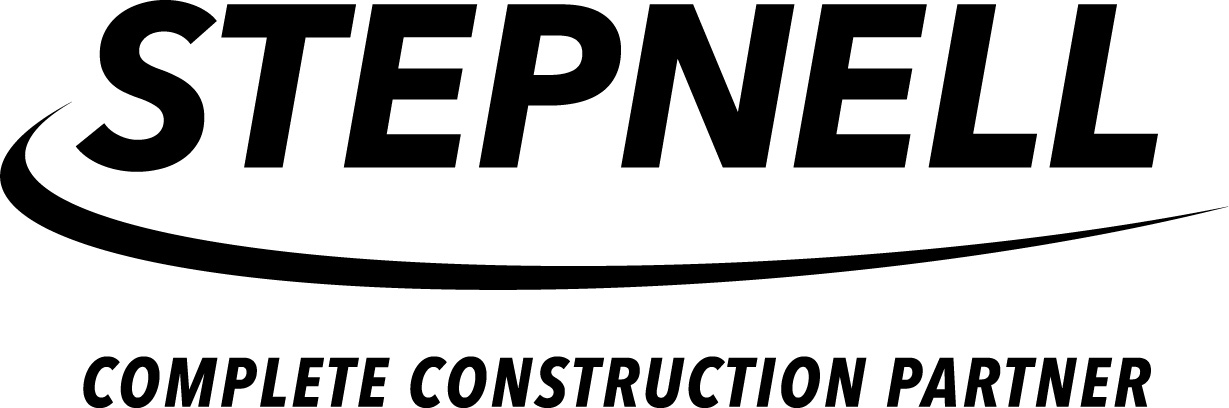
Stepnell’s BIM approach; ‘no stone unturned’ for University of Worcester
The digital journey from construction through to facilities management This is a story of using multiple technologies on a refurbishment and extension project— gaining maximum insight and value from a Revit 3D model, streamlining workflows, format... Learn more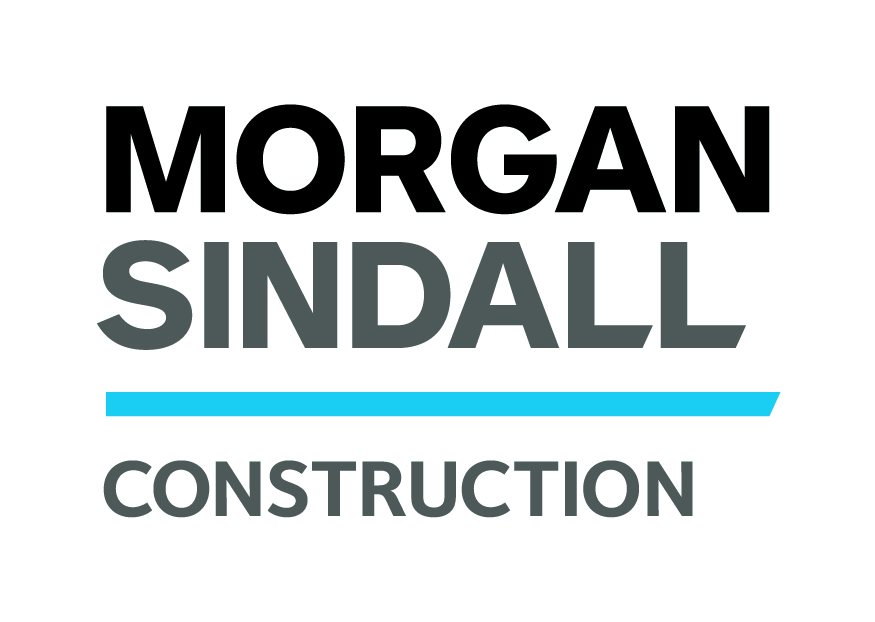