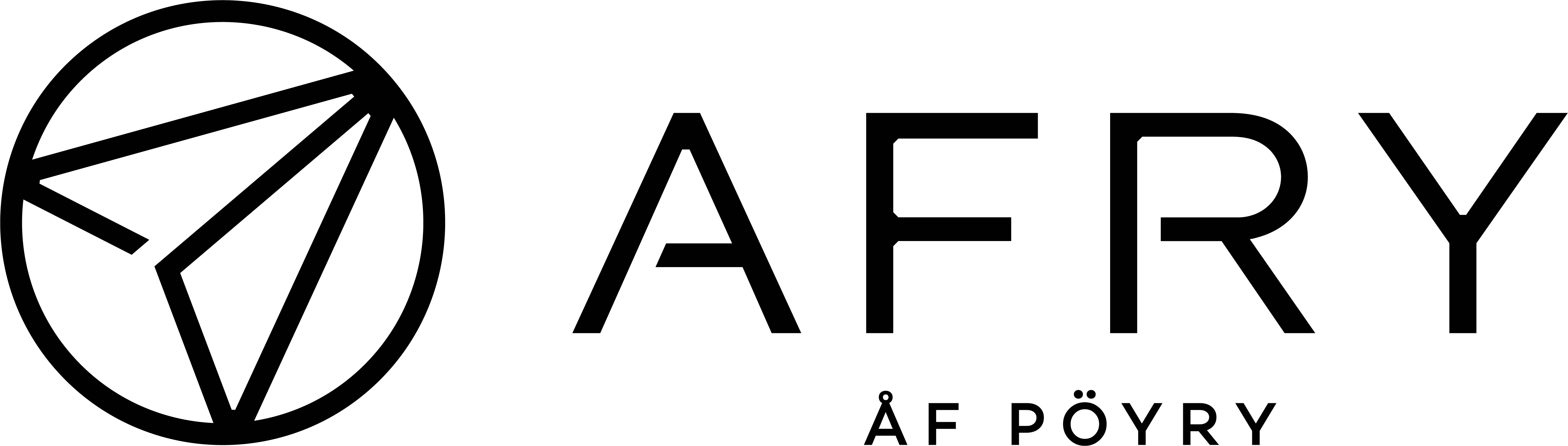
Digital simulation reduces costs and shortens time from plan to product at EKOVENT

Using Simulation CFD software from Autodesk, a product’s pressure drop can quickly be simulated and verified at an early stage in that product’s development, a procedure that previously was time-consuming and expensive.
Simulation is a way of imitating reality as closely as possible in a virtual environment, with the CAD-model being the heart of the process. It can be said to be the creation of a digital prototype where sensors can be positioned at a later stage, and it facilitates visualisation. The purpose for the user is to be able to more easily visualise the finished construction long before actual completion.
"Drops in pressure in a building’s ventilation cost both energy and money. Property owners naturally have a great interest in operating energy-efficient buildings, with energy savings having environmental as well as financial benefits. Digital simulation presents major opportunities for EKOVENT in comparison to how they worked before. Now the software allows us to test and verify a product’s pressure drop at an early stage and it’s easy to try out several product variants in order to find the optimal one,” says Henrik Augustsson, one of the engineers who works with product development.
From slow and expensive to fast and cost-effective
For several years, EKOVENT has wanted to invest in a simulation product but the expense has been a deterrent. Thanks to Simulation CFD from Autodesk, the price came down to a reasonable level,” explains Henrik Augustsson.
The previous process was expensive as well as time-consuming. Firstly, a product was designed, with calculations being made of air flow and pressure drop. Then a prototype was produced and sent to the Swedish Technical Research Institute for testing, which was a slow, expensive process. When the results came back they were evaluated and, if we were unlucky, the process had to be repeated several times until the product met our specifications. All pressure drop simulations can now be performed digitally, saving a lot of time and money.
Major financial and environmental benefits
It is not only during the development of new products that simulation can be used. Henrik Augustsson and his colleagues, all of whom use Autodesk Product Design Suite, of which Inventor is a part, see considerable possibilities for optimising their existing products."There are great financial and environmental gains in making our products more energy-efficient. It means, for example, that property owners can reduce the size of fans in ventilation systems, thus decreasing operating costs and environmental impact. We can also optimise material usage in manufacturing the products. If we can reduce the amount of metal in a damper, we can lower the price and also make less of an environmental impact.”
Supplier to Facebook’s data centre in Luleå
The company’s success is apparent from the many exciting projects for which it is designing and supplying products. One of these is Facebook’s data centre in Luleå, Sweden, the largest of its kind in Europe and destined to handle much of the traffic from the world’s 800 million Facebook users. The building covers 84,000 m2, equivalent to more than 11 football pitches, and contains two 144- metre long walls full of EKOVENT products. These extract hot air in order to create a favourable climate for the mass of computers producing heat in the centre.
Another well-known project is Friends Arena, Sweden’s new national arena that accommodates up to 65,000 spectators. The retractable roof allows events to take place all year-round, regardless of weather. EKOVENT has supplied this project with fire, smoke, iris, control and shut-off dampers.
Symetri support and know-how
In order to learn how to best use the simulation product, all of EKOVENT’s engineers have undergone training at Symetri. Thereafter, EKOVENT has worked tirelessly on continuous improvement with the help of Symetri, who are always interested in being updated about progress and how we work with the tools.
Leave us a message
Related Cases
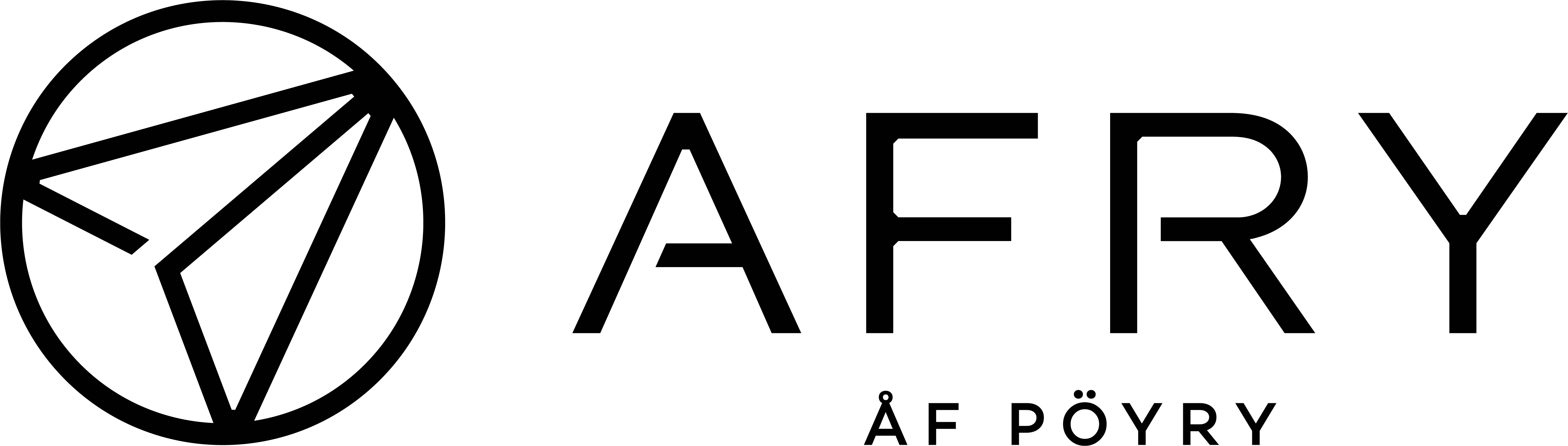
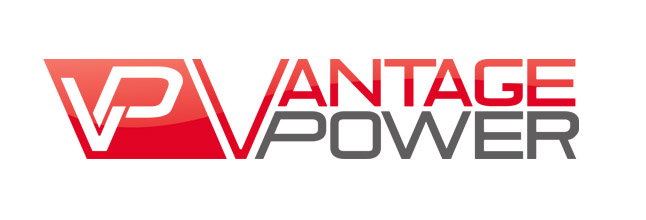
Innovative business decisions are supported by unique technology solutions
By designing an entire hybrid system for buses – covering everything between the fuel tank and the wheels with optimal performance of every component, Vantage Power has created a system that results in higher fuel economy, lower emissions and grea... Learn more